国内的精益生产实践处于什么水平?
国内的很多制造企业之所以对“精益生产”持怀疑甚至否度态度,大都经历过实施过程中的“水土不服”难题。抛砖引玉讲一下:
1、精益生产的最典型案例
1991年,在当时整个美国处于一种将被“日本人支配”的恐惧背景下,“精益生产”一词问世。
它源于的是丰田的一种内部管理哲学——这个独到的管理哲学的践行,让丰田一举超越美国和欧洲并占据汽车行业领先地位,超过美国福特和通用的总和,到 2007 年其汽车销量全球第一,在世界的汽车舞台上独占鳌头。不仅如此,日本国内的其他产业(飞机,造船,钢铁,化工和电子通讯领域等)应用精益生产管理方面都纷纷取得成功。
在这种恐慌下,美国Womack研究小组耗费了5年时间:走访各大汽车厂家、实地调研汽车工业,手握详实资料写出了《改变世界的机器》一书,正式把丰田生产方式确定成为精益生产方式,说明从大量生产方式转变到精益生产方式的必要性。
它的精髓在于“精益”二字,通过自动化、少人化,、准时化、小批量、多品种、消除七大浪费,从而降低成本。尤为注重持续改进和尊重、员工团队合作。
(展开说,就是通过系统结构、人员组织、运行方式和市场供求等方面的变革, 使生产系统较快适应用户需求的变化,并使生产过程中一切无用、多余的东西被精简,达到包括市场供销在内的生产各方面最优结果的一种生产管理方式。)
举个例子,当精益运用到成本管理中,那精益成本的概念与以往的成本概念会有所不同:
售价=成本+利润(计划经济) 售价-成本=利润(市场经济) 售价-利润=成本(精益成本)
体现出了精益成本的核心:成本的降低取决于制造方法的改善。
2、中小型制造企业“精益生产”是否有必要
普遍来看,制造业中小企业因为生产成本难以下降,而瞄上了“精益生产”。
举个例子:
某汽车零配件制造公司一件售价为10元的汽车零配件,其中的采 购成本为7.5元,剩下的2.5元包括企业生产运作、设备投入、员工工资、企业管理 费用等等。正是因为管理成本下不去,造成企业的生产利润极低,每件产品的利润只有5%左右,如果发生交货延期或者产品品质问题,每件产品的利润甚至远远低于5%。
因此,对于这家公司来说,保证企业利润,必须进行良好的生产管理,降低废次品率,保证按期交货。
但众多中小企业在生产制造中,还有很多问题:
- 员工素质不高,对企业的生产管理制度理解不透彻,执行不到位;
- 生产管理现场混乱,没有进行5S和目视化管理,材料堆放随意,堆放过程中造成零部件和在制品损坏,生产过程中零部件和在制品找寻成本过高。;
- 很多中小企业还没有建立一套科学的质量管理体系和产品质量管理不到位。虽然大多数中小企业都通过了ISO 质量管理体系审核并获得认证,在今天的市场上,ISO只是一个基本的企业质量管理体系。许多中小企业没有在实际管理相应的管理。他们的生产和质量管理的质量管理体系还不是很规范。
- ……
这个时候,精益生产是极具价值的,但前提是,是成功的“精益生产”。
3、成功的“精益生产”
“精益生产”发展至今,在许多企业挣扎下,多少都尝到了“精益生产”的甜头:
福特通过FPS 模式,在生产过程中,充分利用企业资源,提高生产效率; 丰田通过TPS 模式,创造了高质量、低消耗的生产方式; 海尔 “人单合一双赢模式”实现了先为客户创造价值再实现自身价值的双重效果,鼓励员工自主创新; 美的 “T+3 计划优 化”通过产销供联动压缩供货周期,提高效率。
但精益生产引入国内,经历了很长一段时间的水土不服,在上世纪 70~80 年代,“精益生产”就被引入国内——当时长春一汽通过外派人员去日本丰田企业交流学习后,回厂着手实践精益生产模式的运行。
但当时正值计划经济体制的约束,导致精益生产方式不被大众所接受和理解,加之企业传统思想的影响,精益生产未能获得较大成效。
因此,要不想重蹈覆辙,“精益思想”要到位:
1)精益不等于裁减人员,而是消除浪费,实现低投入高产出,可能有小幅度的裁员,但并不是一味地裁员。
2)一旦领导者放弃发展精益管理,则企业难以走上精益之路,更难以得到更大的发展。企业的管理者要知道,精益管理不是大企业才需要的管理方法,规模较小、人员较少的中小企业同样需要。
3)很多中小企业在短期实施精益生产方式后,看不到明显增益的效果就认为自己企业不适合经济管理,从而舍弃精益管理方式;又或者在实 施精益管理得到一定的成果后,满足于现状而不进行更深入的精益改革,遏制了企业的进一步发展。这是因为员工与领导者缺乏对精益思想的认可和深入认知。
4)企业在精益管理实施过程中生搬硬套模式,滥用精益方法。有些中小企业在实施精益管理模式时,并没有充分调查企业自身情况,就把所有的精益管理技术方法都运用到企业中,或仅使用某一种精益管理技术方法,把精益模式与精益方法之间的逻辑关系割裂或错误的搭配,最后导致企业实施精益管理的活动混乱地进行,难以达到理想中的精益管理效果。
5)企业在实施精益管理后,不能及时地对精益的实施进行考核评估,造成精益效果不能持续有效。缺乏精益的考核评估,会容易淡忘精益做法和精益目标,没有动力坚持精益改革;也不能及时地发现和解决精益改革实施存在的问题, 得不到员工的精益反馈,这样不利于企业的持续改善和发展。
精益思想到位后,成功的“精益生产”,还会用到几个工具。
4、可以帮到你的几个工具
1)5S
以目视化、简洁、整齐为基础的现场管理系统。5S管理的每个环节内容分别为:
- 整理:对于工作现场的要与不需要的物品进行区分,然后清理掉现场不需要的物品;
- 整顿:将现场的物品定位摆放整齐,归类明确,标识清晰;
- 清扫:将现场清理干净,保持现场整洁;
- 清洁:在清洁的基础上建立规范制度,维持取得成果;
- 素养:通过对员工进行培训管理,形成良好习惯,改善和提高个人素养。
2)准时化生产
准时化生产方式的核心是追求一种最小库存的生产系统。以客户为中心,前工序根据后工序的信息安排生产,由后工序拉动整个生产节奏,减少库存和生产环节浪费,实现整个生产线的平衡。
3)看板
看板管理就是生产现场的物料移动显示器,也是实施准时化生产的基础,在物料的移动中看板信息会不断的发生变化,这样形成实物与信息同步,先后工序保持平稳均衡,从而实现准时化的生产目标。
比如,某汽车零部件有限公司的【模具管理】看板,帮助他们实时监控模具状态、报修次数、报修原因等:
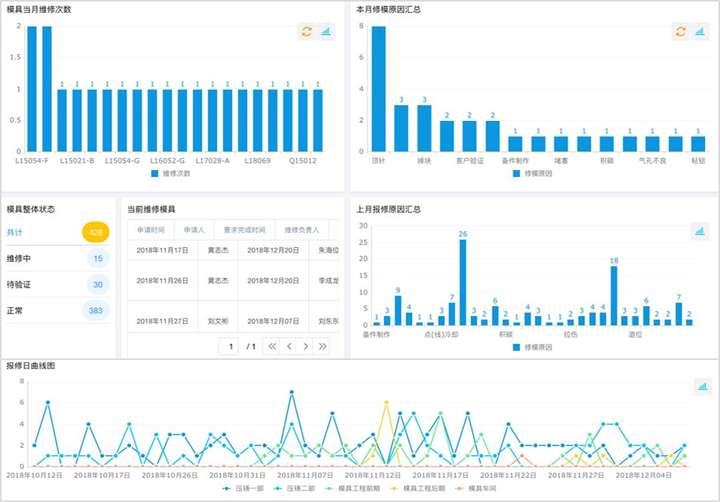
看板来源:【简道云】上搭建的模具管理应用
4)生产线平衡
对生产线的全部工序进行负荷分析,通过调整工序间的负荷分配使各工序达到能力平衡(作业时间尽可能相近)的技术手段与方法,最终消除各种等待浪费现象,提高生产线的整体效率。这种改善工序间的能力,使之平衡的方法又称为“瓶颈改善”。
5)单件流
单件流是指各工序只有一个工件在流动,是一种最小批量的生产方式。整个过程是不停滞、不堆积、不超越的流动状态,这个方式可以使问题逐步的暴露出来,然后主动解决问题,有利于不断持续的改善。
6)单元生产
单元生产是一种精益生产方式,其核心要素是单件流。通过该手段实现少人化的生产制造。是践行精益生产的关键。该方式适合多品种、多批次、小批量、短交期、定制化、更新快的市场需求。在这种生产方式下,可以发挥员工的主动性,实施独立单元作业避免产品堆积产生,提高生产效率。
7)价值流图
价值流图是对信息流,物流,工艺流的整体可视化描述的方式。一般处理问题是会使用当前价值流图来分析问题,找出实际生产模式下整个流程中信息流,物流和产品工艺流的具体情况,记录并分析相关浪费信息。根据问题点进行设计新的整改计划,这样制定出新的未来价值流图。该图是一个宏观角度分析整体生产状况的工具。
8)全面生产维护TPM
全面生产维护特点是全效率、全系统、全员参与。三者之间的关系是:全员参与是基础,全系统是载体,全效率是目标。 全系统是指生产现场的设备维护不仅仅是设备部门的事情。生产、技术、安全、质量、工程、财务、人力资源等各个部门都要参与其中。全效率指设备综合效率和寿命周期费用评价。全员参与是指从企业最高管理层领导到一线生产岗位人员都参与。
文中涉及工具:
